...has a nice ring to it, eh? "Man of Titanium" is not bad, he's probably a fitter, leaner, stronger version of the first bloke, right?
But "Man of 7075-T6" sounds pretty crap, although in many ways he's somewhere between the two.
"WTF?" I hear you ask. How do I know you're asking this? Because my good lady often has the very same look on her face that you do, and she's not shy about telling me why.
So, backing up the bus, 7075 is an alloy of aluminium. Compared to common old 6061, 7075 is made by adding a touch more zinc and a smidge of magnesium, so far so boring, its properties aren't hugely altered. But the magic happens when 7075 is tempered (the T6 tacked on the end) during the alloying process.
It turns out "homogenizing the cast 7075 at 450 °C for several hours, quenching, and then ageing at 120 °C for 24 hours" creates an alloy that is 1/3 the weight of steel yet is stronger than some of the steel alloys. You might know this wonder material as "Ergal".
Hmmm, I'm sensing some bullshitometers going nuts right about now, but check this out:
Tensile strength (MPa) Density (g/cm3)
6061 310 2.7
7075-T6 572 2.8
mild steel (ASTM A36) 400-550 7.8
304 stainless steel 621 8.0
6AL-4V Titanium 950 4.4
Obviously there are a heap of different properties involved and each material has its advantages. For example, most of the above can be welded but 7075-T6 not so much as it tends to crack, similarly casting removes the temper so is a no go. But its combination of high strength, low weight and corrosion resistance make it a no-brainer for aviation/aerospace components.....and Ducati parts.
I could have said "motorcycles" in general, but realistically the parts just aren't out there for most bikes, but the good folks in the Ducati race department seem to be unique in producing almost everything that wasn't carbon, titanium, or magnesium, in Ergal. Which is a round the houses way of explaining why a parcel arrived the other day with what is effectively an aluminium swingarm pivot shaft.....that is "stronger than steel" and 1/3 the weight.
Apologies, I'm at work so I can't weigh it, but this is what I'm talking about, pictured amongst the rest of a rare Corse 999RS/F0 swingarm kit (no, none of it mine) :
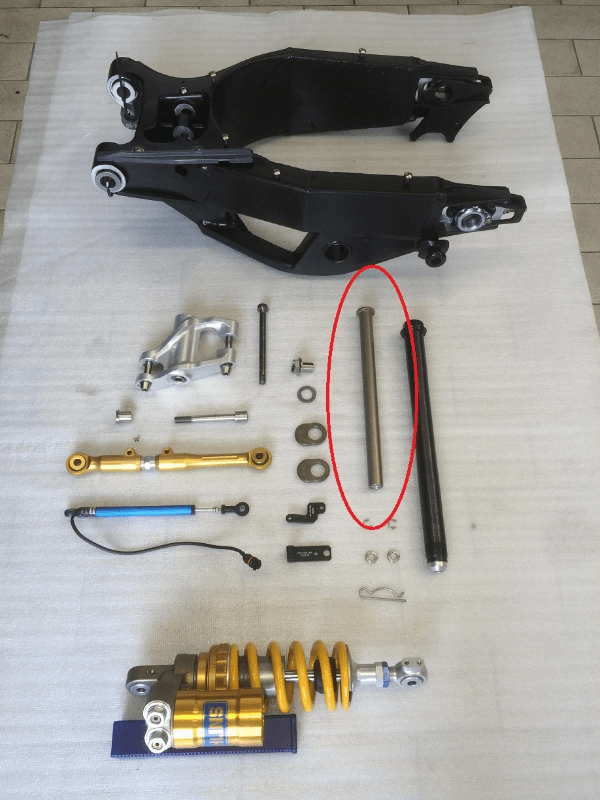
And like virtually all Corse parts it's etched with the part number and manufacturing date:
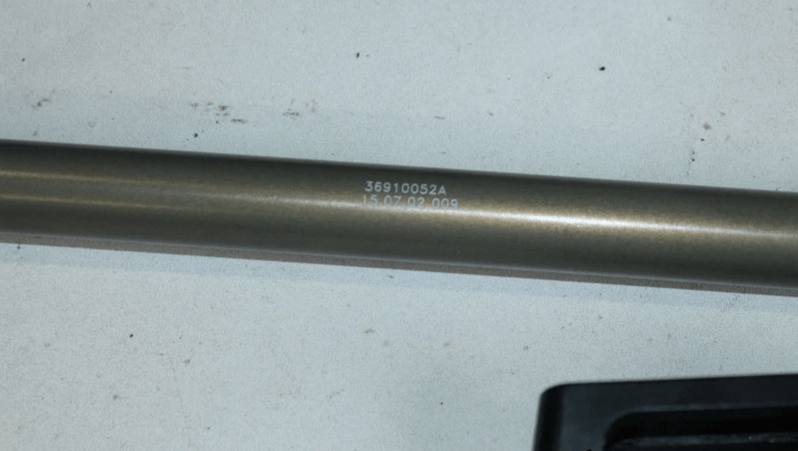
FYI, this pivot shaft is common to everything from the Tamburini 748/9*6/998 through to the Terblanche 749/999, hence the pre-999 2002 manufacturing date is no issue.
I'm pretty chuffed to be eliminating such a large chunk of steel. The only problem is the shaft bolt -there isn't one:
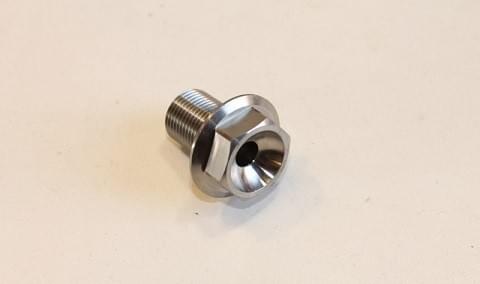
Now I have a few options here:
- Heavy OEM steel, costs nothing 'cos I have one, but seems a bit crass against the featherweight pivot shaft.
- I know where there is a brand new Corse Ti unit available, that cute lil' fella just above....for 135euro. Hmmmm, not so cute now, eh?
- An alternative Ti M15 flanged bolt, (bicycle crank set are a common application), fairly inexpensive.....except after turning over every rock on the internet I can only find 1.0mm pitch, where I need 1.25mm. Bugger.
But what's the point of using an expensive uber-tough Ti bolt given the aluminium it will be threaded into? So some Ergal round bar is winging its way towards me. It's fiddly but we'll have a crack at machining something more appropriate and even lighter than Ti, it's not like a WSBK application where it's going to get chewed up being taken on/off several times a weekend.
It all gets a bloke, even a not so smart one, thinking: how many of those other expensive Ti bolts could be Ergal? Not only would they be substantially lighter, but substantially cheaper and what's not to like about that? They'll be no worse than the OEM steel bolts and perfectly adequate in most cases.
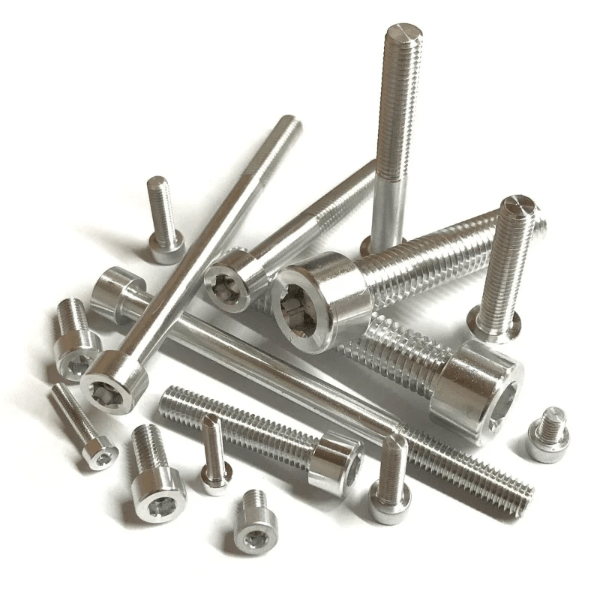
It makes you think eh? Especially when you're using a Ti bolt to secure a relatively flimsy piece of carbon fibre/plastic etc.....it just doesn't seem smart, and being an expert in the field of not being smart, I should know! I've trialled some 6061 bolts for that sort of thing in the past, but the material is so soft they are almost single time use as the heads almost instantly burr up, or worse, round off, so it was lesson soon learned....but Ergal might just be the perfect solution.
Ultimately it's horses for courses: Ergal has an Ultimate Tensile Strength equivalent to steel but it does have a significantly lower Yield Point (the point at which it is permanently deformed).
But even Titanium has its limitations, being quite brittle so applications subject to flexing are prone to breakage. Ti is also very "notch sensitive", where a small surface imperfection propogates to a major failure. Both of which explain why Titanium axles are verboten by most racing governing bodies.
There is another, more insidious, issue with Titanium....
This is a trackbike that is going to be swaddled in mink furs, cosseted away from all harmful elements while reclining elegantly on a chaise lounge in my mechanical boudoir. Which is handy given Titanium is at the opposite end of the galvanic scale compared to aluminium and steel, meaning it has a far greater propensity for galvanic corrosion. Add LinkAdd Alt Text
Galvanic corrosion? If you have 2 dissimilar metals against each other, add moisture and you are effectively adding electrolyte to a battery = current flow = galvanic corrosion. The further apart the metals on the galvanic table the greater the current flow and greater the corrosion. So how far apart are titanium, aluminium and steel? This far:
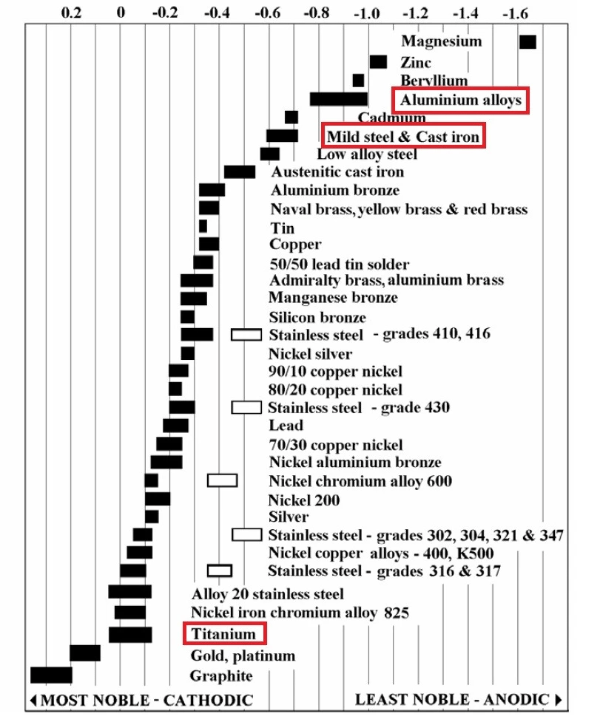
Or, like the girl next door all grown up, suddenly that plain-Jane steel is looking quite attractive!
Anyway, just some food for thought if you are looking at replacing fasteners etc.
Speaking of fasteners, this is one example that has always been sand in my crack:
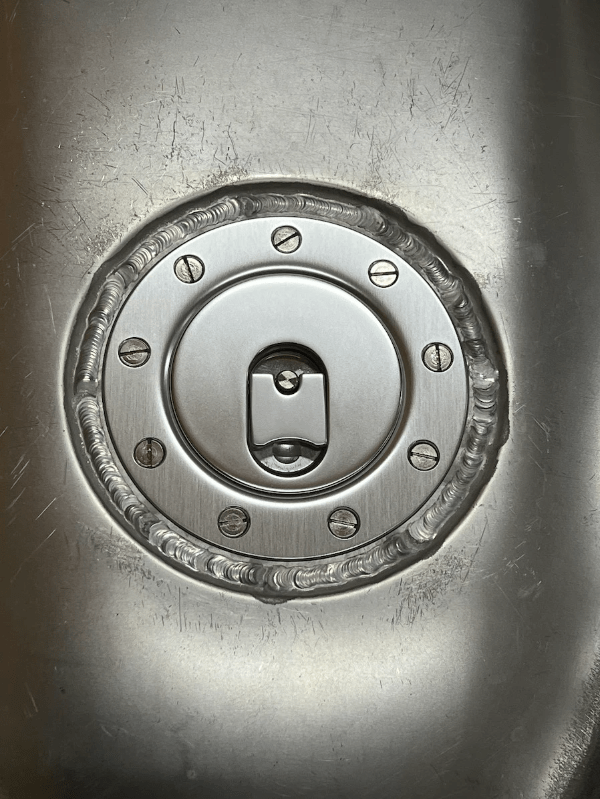
Every time I looked at the slotted screws securing the 799RS fuel cap I'd think "woodwork screws"....every. single. time. I'm not particularly OCD, but something about slotted screws/bolts on a modern bike makes a vein bulge in my forehead. In this case they are stainless but even if gold plated they'd still be destined for the "miscellaneous bolts" biscuit tin.
You can tell this pre-dates my self-paced learning above, because some Ti socket head bolts replaced them, soothing my mechanical hackles:
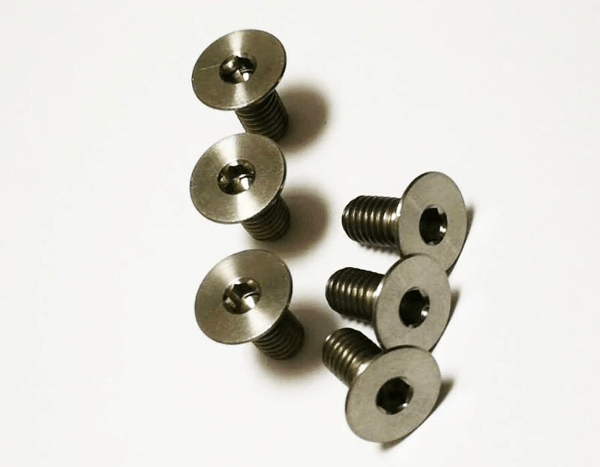
...and all is right with the world. Yes, I know, a classic non-structural application where Ergal would be the absolute dog's danglers, but it's a lot better than wood screws, innit?:

Looking at the above brings me to another pain in the arse: welding.
I'm finding myself regularly bumping into an aluminium ceiling: I can't progress jobs without some form of aluminium welding, be it a broken tab on the 851 oil cooler, the alterations required for the 799RS dash mount/fairing brace, the swingarm modification, an exhaust mounting bracket on the subframe, reconfiguring the mounts on the 799RS MB Motorsport oil cooler/radiator arrangement, an alloy lathe handle broken in transit etc etc.
But I don't have the gear to weld aluminium, nor do I have the skills, it's enough to drive a man to drink.....er, drink more.
Then, mana from heaven....no, actually more like scant reward for 20 years in purgatory. It came as a pleasant surpise that 20 years service working on the same offshore project in the the Timor Sea...
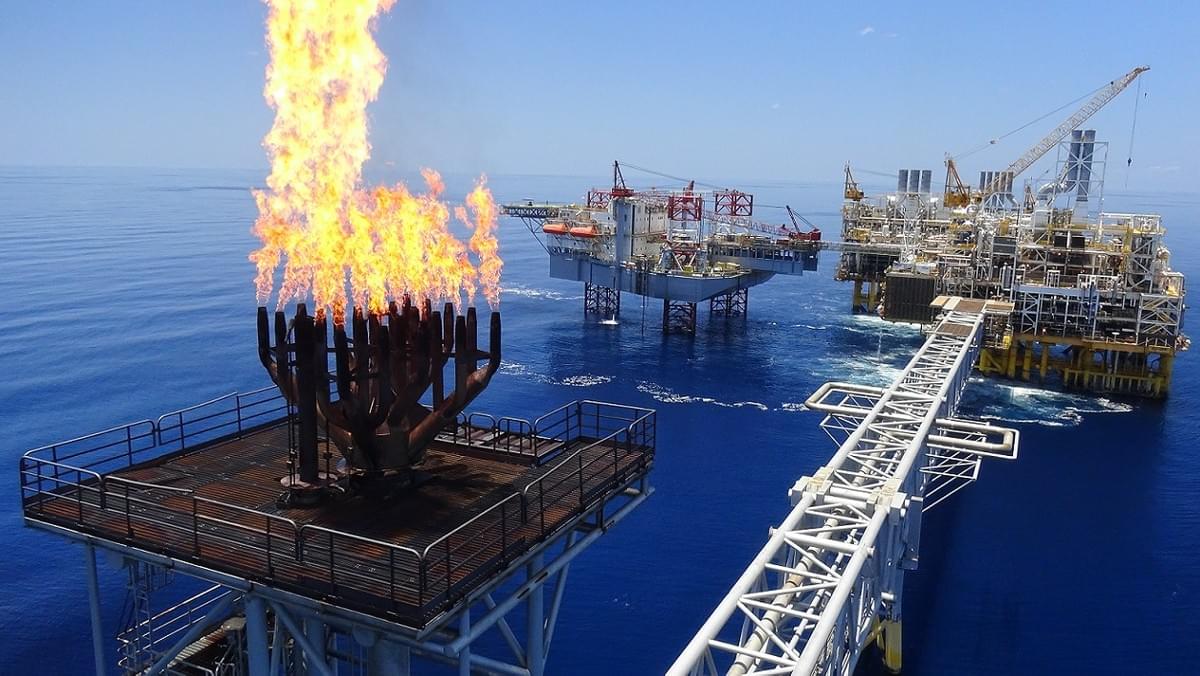
....resulted in a small cash "Service Award" from my employer.
Hmmm, it was bloody hard earned so let's think about this: I could buy myself some sexy undies...or some even sexier bike parts (like putting it towards that WSBK swingarm?) Both of which would be nice.....but not as nice as being able to weld alloy.
So rather than pick up a ghetto-style used TIG/MIG welder as I'd been considering, the service award coincided with a special on this beautiful lil' bundle, which I could never have justified otherwise, a gift that hopefully keeps on giving
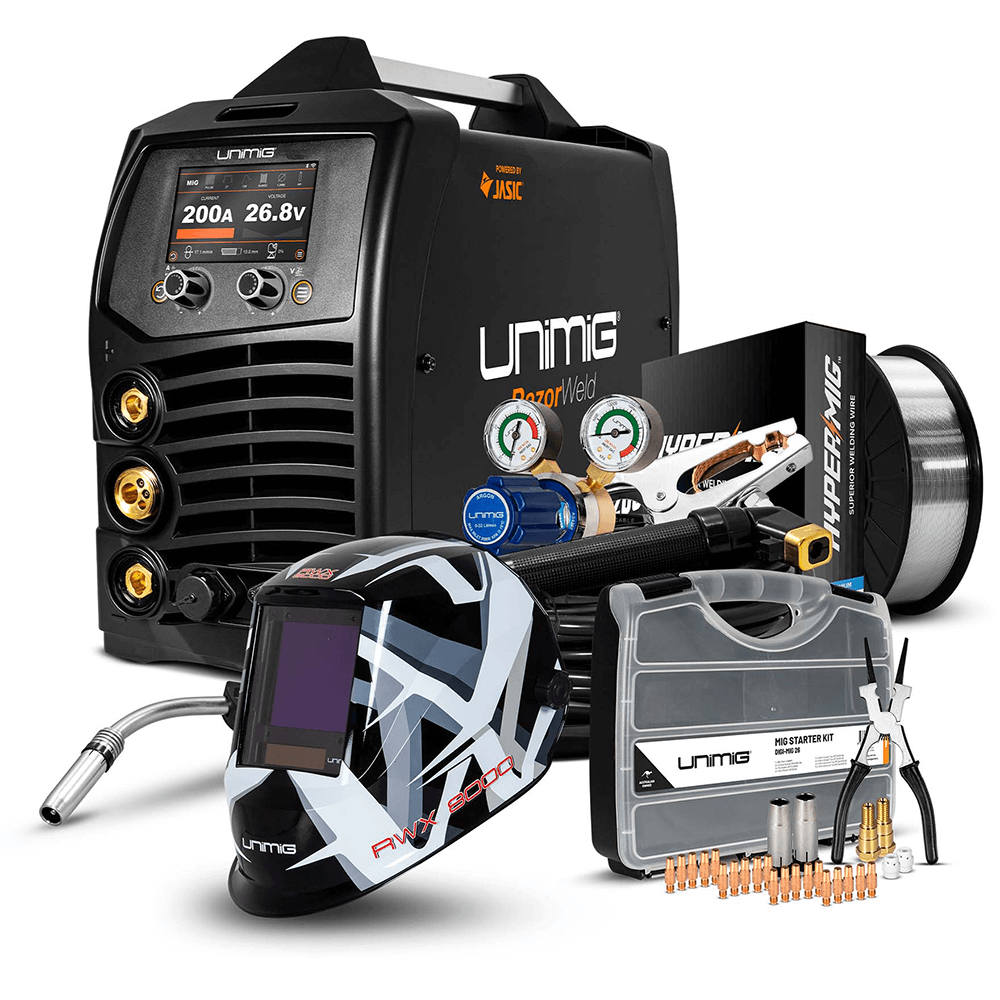
The beauty of this thing (pulse/double pulse MIG/TIG/Stick) for a complete amateur is the "Synergic" setting system: select the material, the thickness, and it automatically configures optimal settings that you can then tweak as you see fit. And the pulse/double pulse feature allows you to MIG weld thin material without putting as much heat into it (= a molten mess) as you otherwise would.
As mentioned, I'm a rank amateur but a few Youtube welding video's on a quiet nightshift, and a quick play prior, and soon enough I'd made a perfectly adequate/solid repair of that broken mount on the 851 oil cooler. You bewdy! Obviously lots more practice ahead before I'm proficient to tackle more visible/structural stuff but you've gotta start somewhere and I'm quietly stoked that I won't be so reliant on outside assistance.
With that in mind, how about some welding porn? Behold the Termignoni "Reparto Corse" exhaust for the WSBK Panigale 1199 F13, with a combination of Titanium and Inox (a flash stainless steel) tubes:
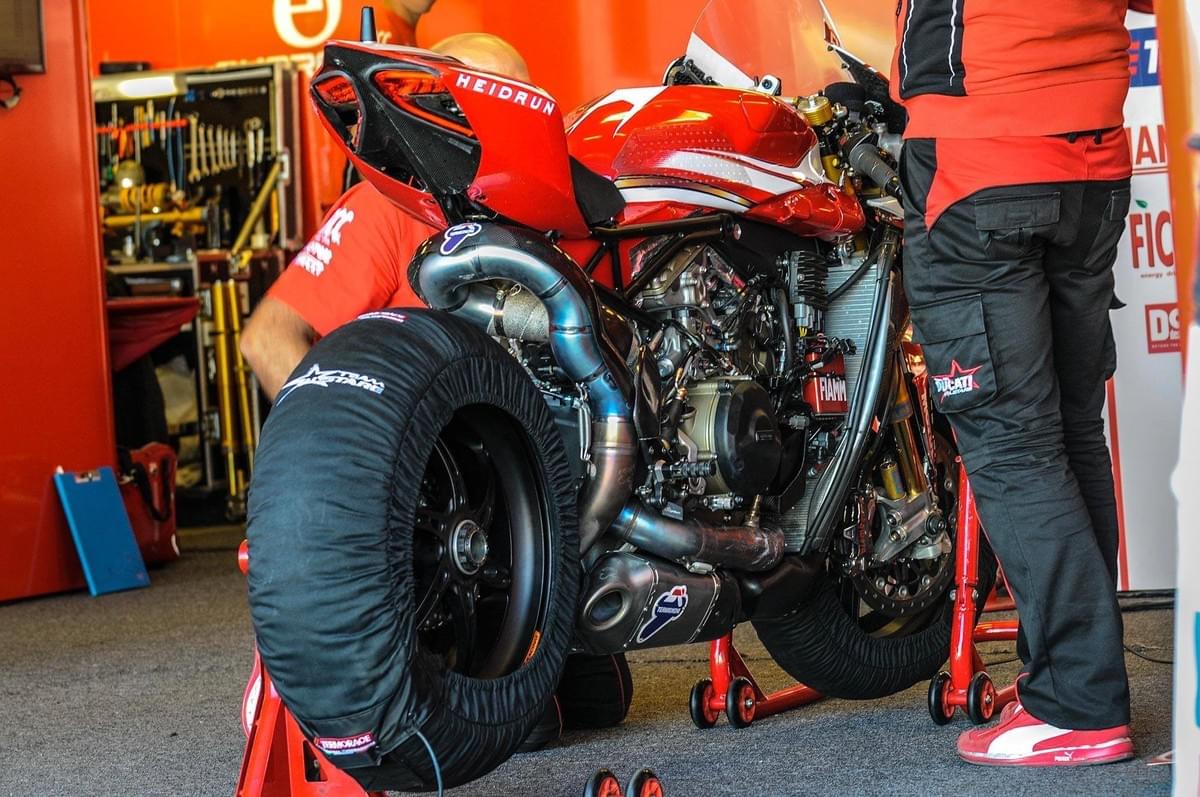
The arrangement is horrendous enough but the difficult materials makes it all the more impressive: Titanium isn't just a bastard to machine, the same poor heat transfer properties make it tricky to weld given it has such a high melting point. It also has an affinity for oxygen and nitrogen, which are absorbed at those high temperatures, causing embrittlement. Think stainless steel's much uglier cousin.
But enough words, the pic's speak for themselves:
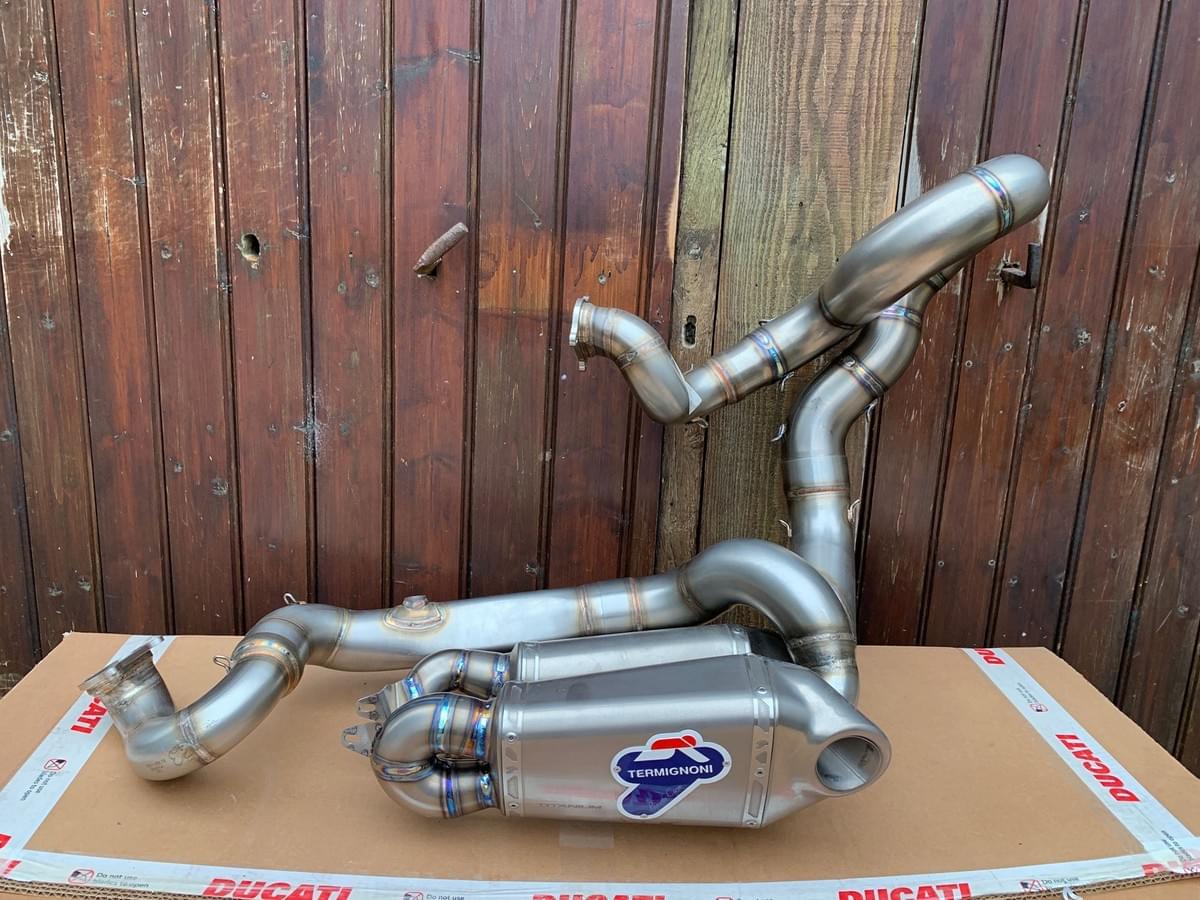
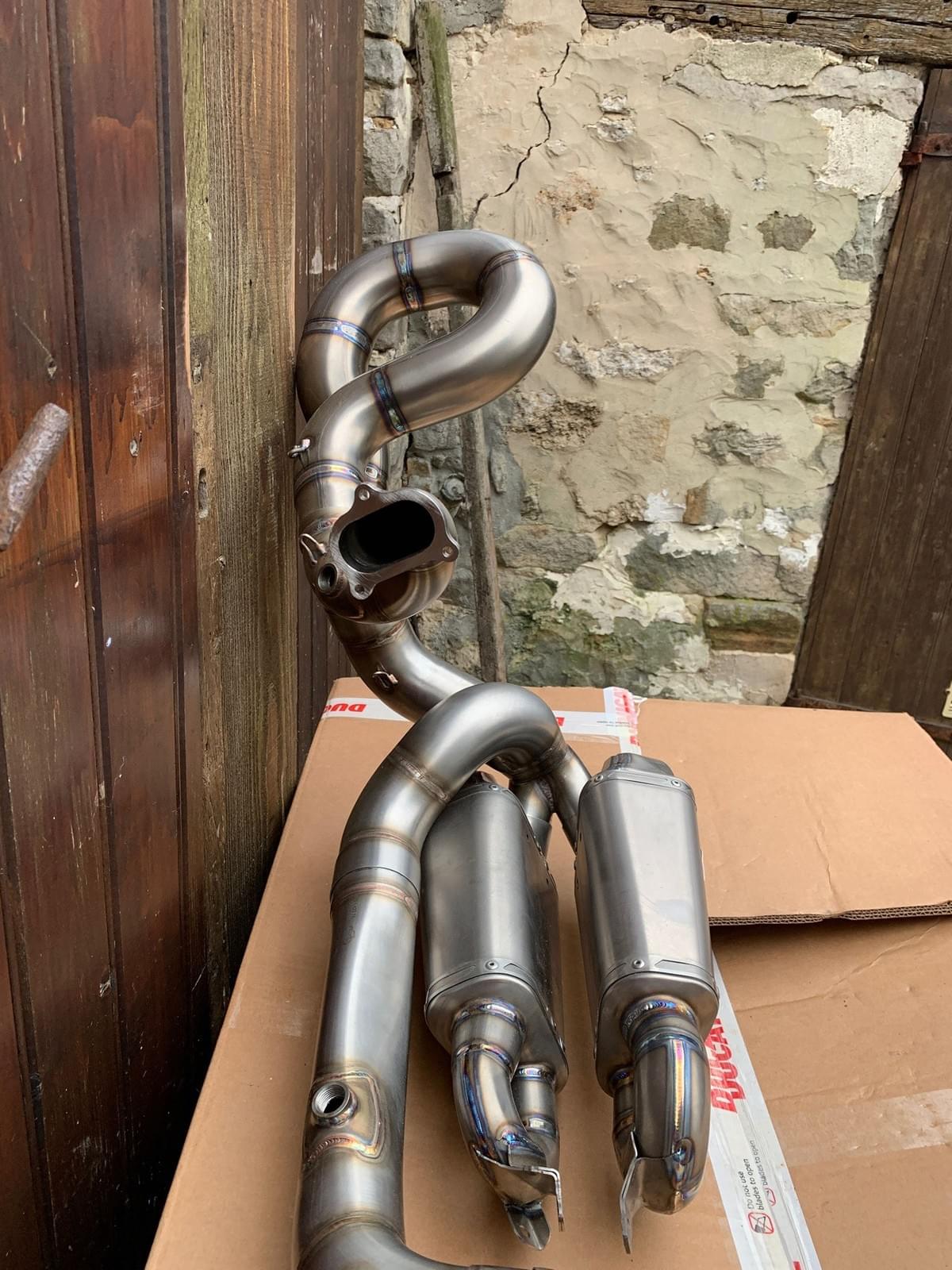
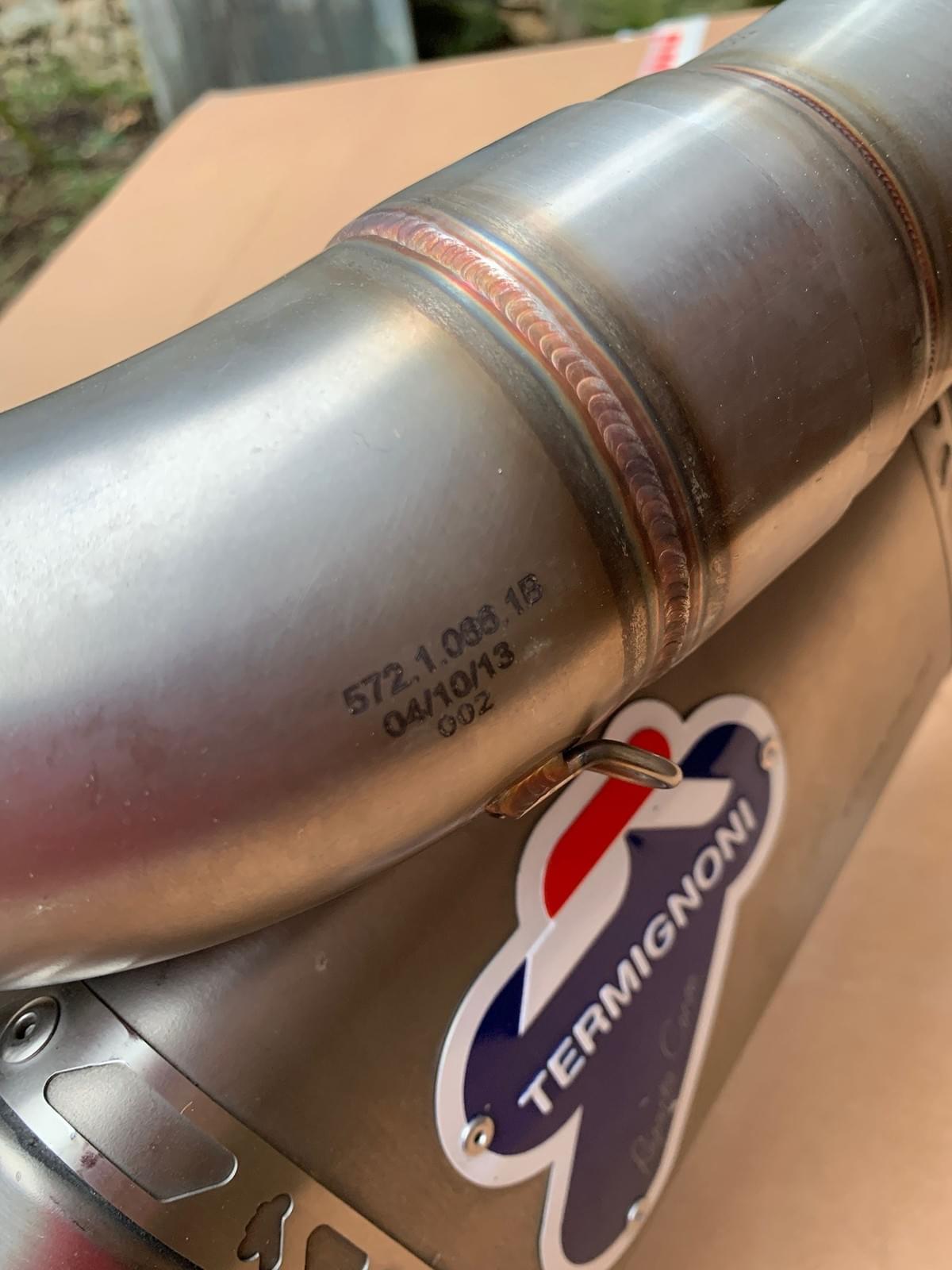
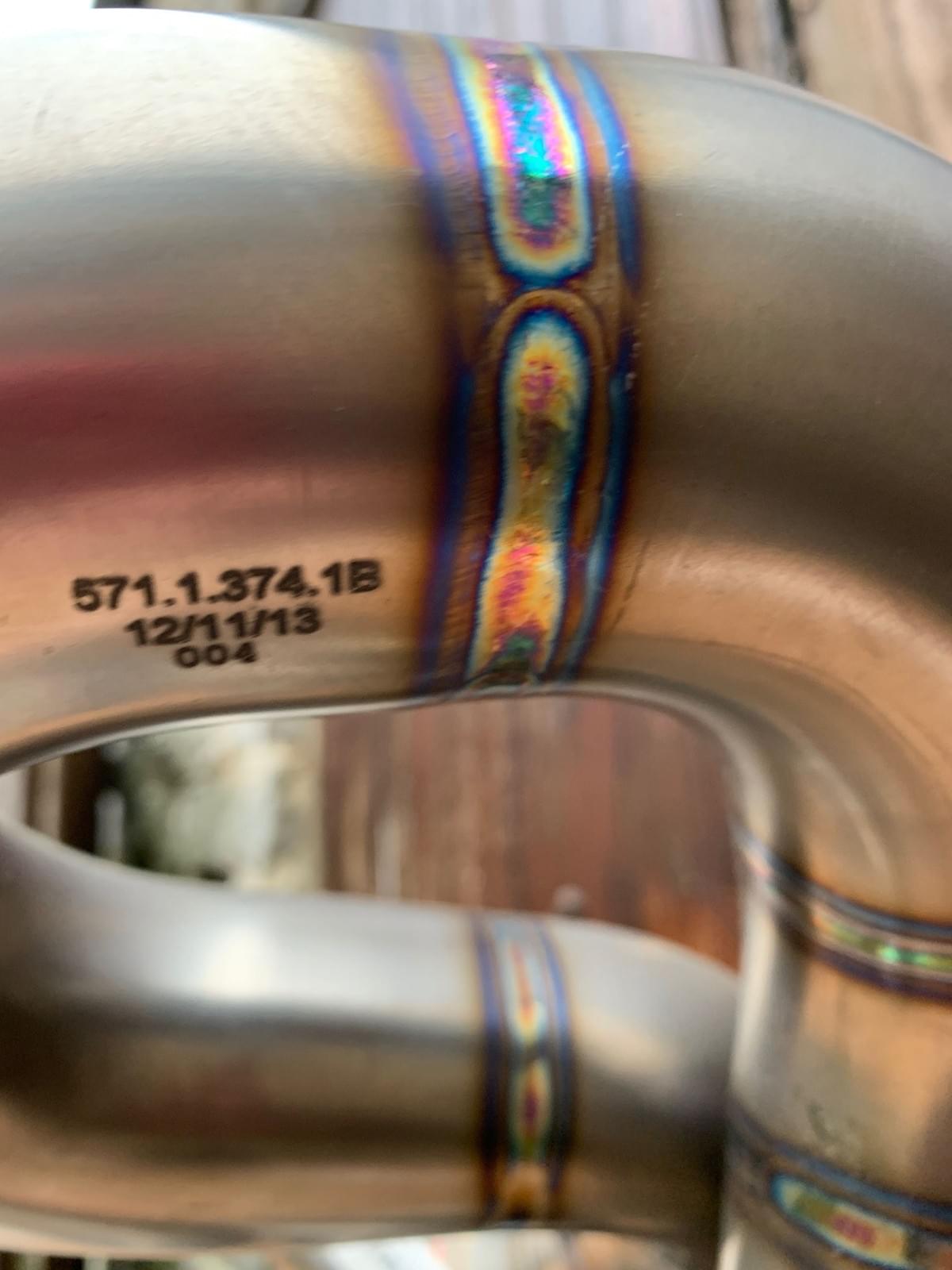
Or, for something even more exotic: a couple of years ago I saw an ex-F1 BMW V10 Inconel header section near auction's-end on Evilbay. I dunno, it just seemed like a lot of "cool" for very little money, so I threw in a cheeky bid for slightly more than the pittance being offered and a couple of weeks later this was sitting in my hands. Some of the welds are verging on invisible:
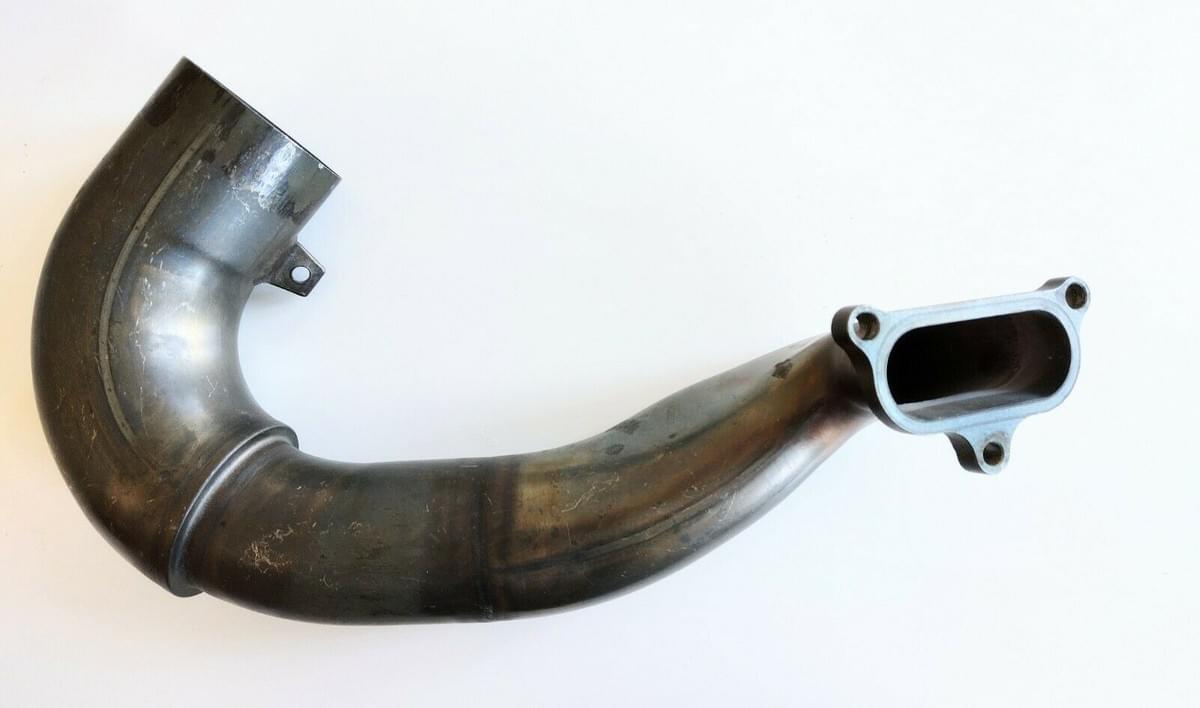
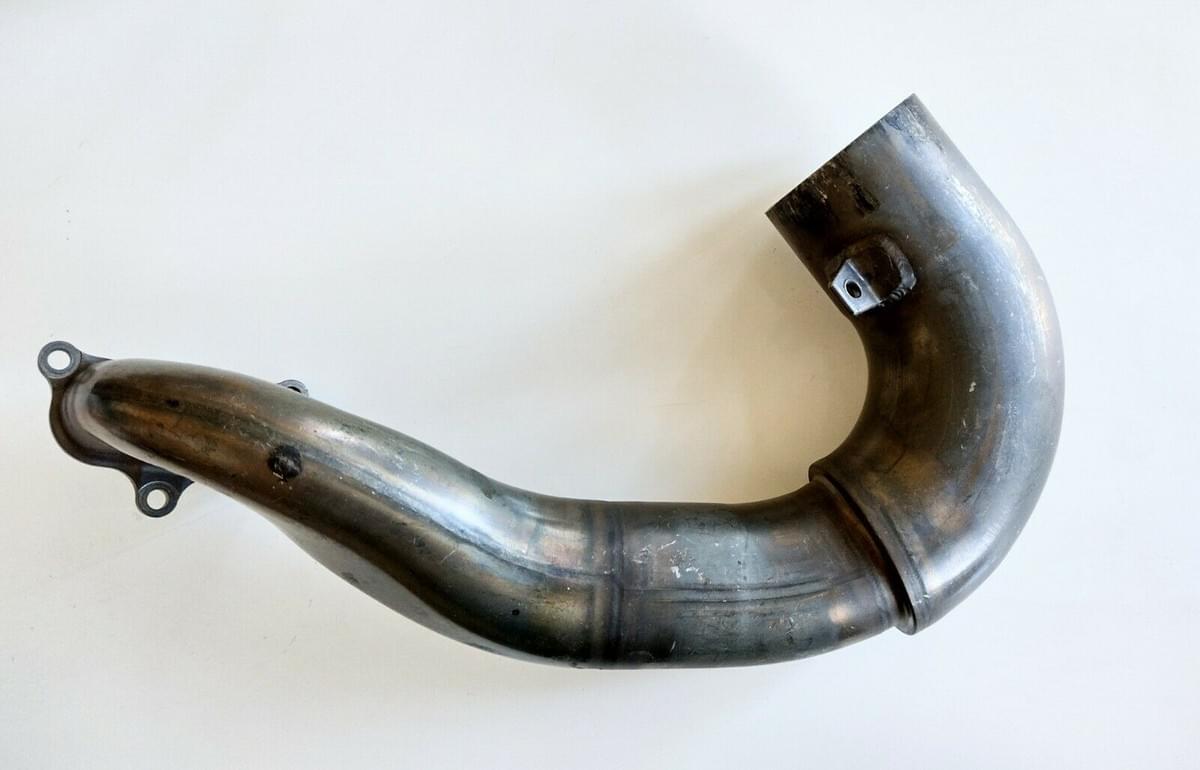

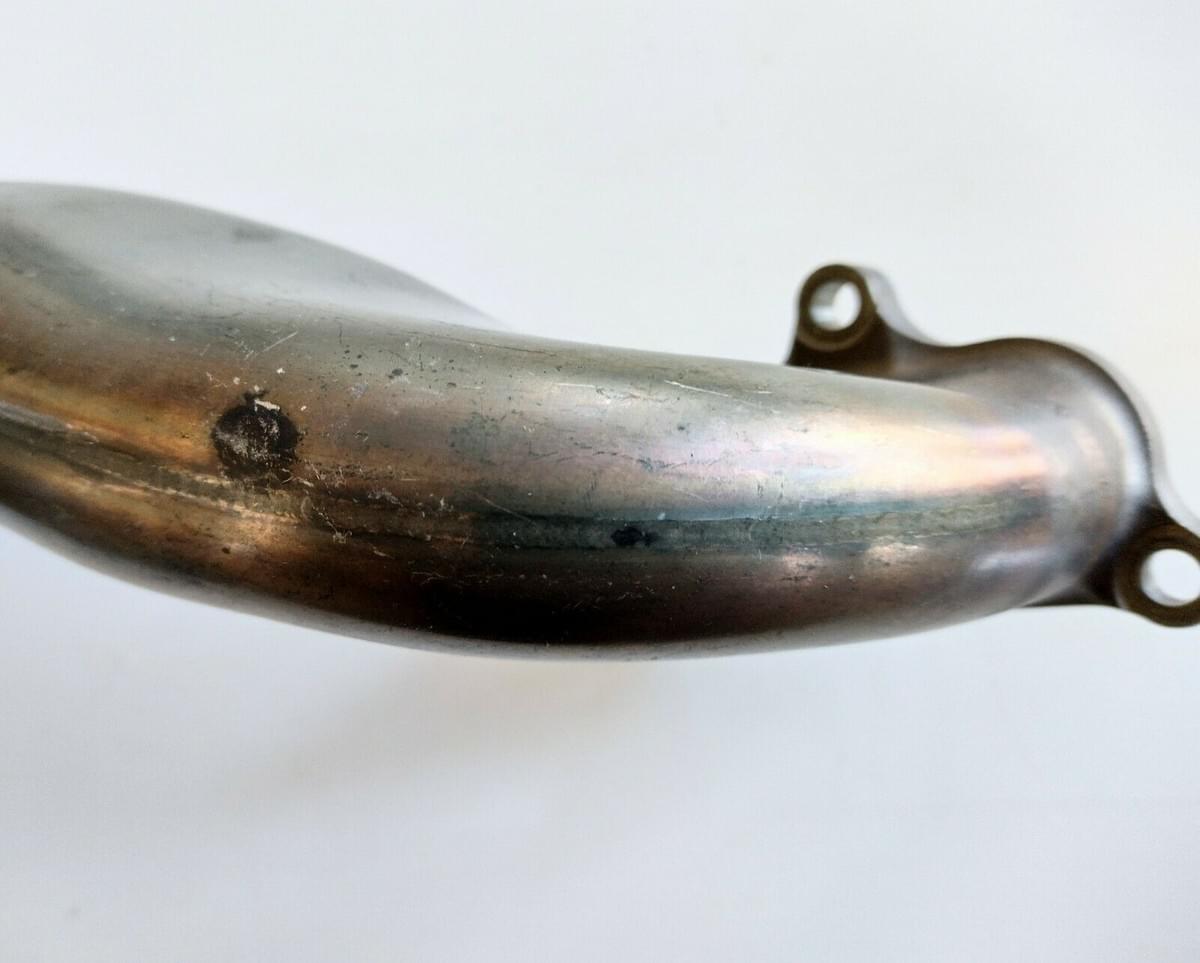
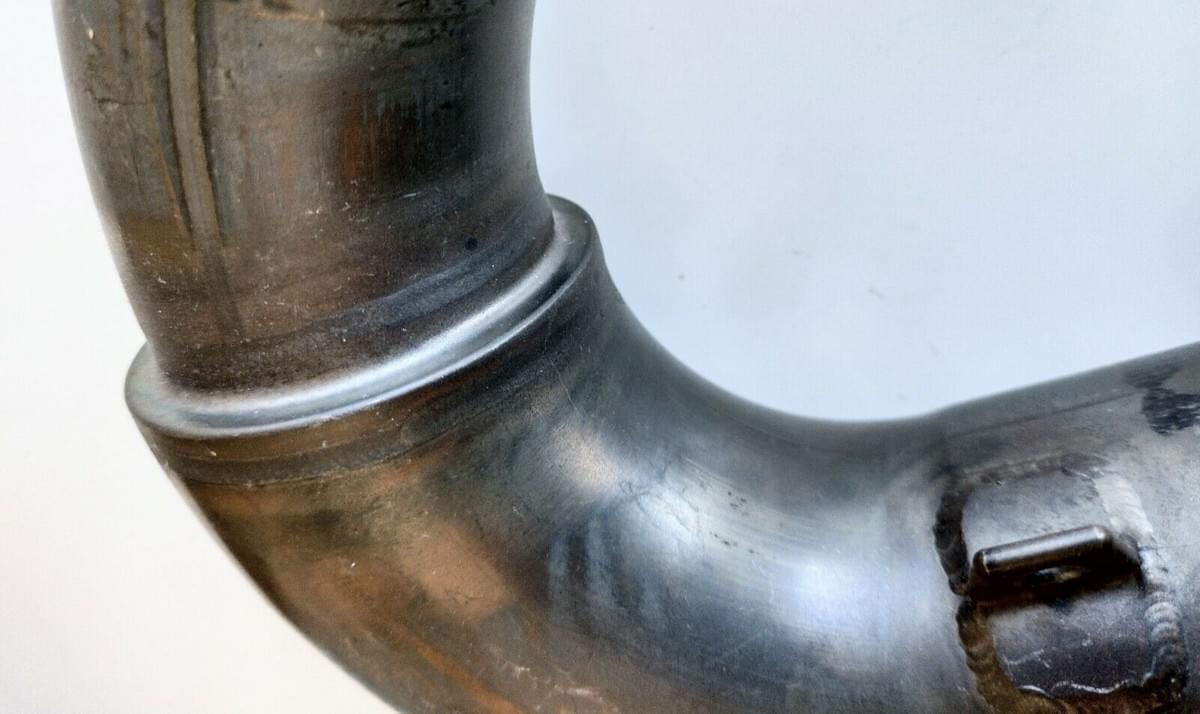
Someone mentioned I should polish it, but I like it exactly as it came off the car even if it does have a few storage marks. F1 leaves me cold these days, but those mighty normally aspirated V10's, revving to 19000rpm, +900hp, were something pretty spesh. Hear one now and they just sound outrageous, where the current V6 hybrids sound as exciting as your washer going through the spin cycle.